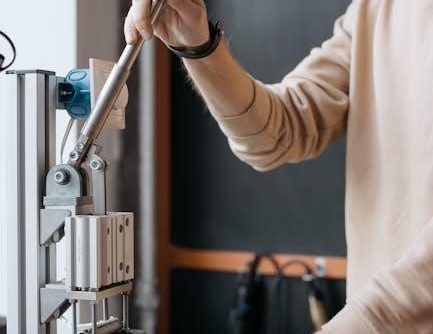
The Manual Handling Hierarchy of Control is a framework to reduce injury risks through systematic control measures. It prioritizes elimination, substitution, engineering controls, administrative controls, and PPE, ensuring a safer working environment.
1.1 Definition and Overview
The Manual Handling Hierarchy of Control is a structured approach to managing risks associated with manual handling tasks. It provides a prioritized framework to eliminate or minimize hazards, ensuring a safer working environment. The hierarchy begins with the most effective control measure—elimination—and progresses through substitution, engineering controls, administrative controls, and finally, personal protective equipment (PPE). This systematic method ensures that employers address hazards at their source, reducing the likelihood of injury. By following this hierarchy, organizations can implement targeted strategies to mitigate risks effectively. This approach aligns with legal and regulatory standards, emphasizing proactive risk management and employee well-being.
1.2 Purpose and Importance
The purpose of the Manual Handling Hierarchy of Control is to provide a clear, step-by-step approach to managing manual handling risks effectively; Its primary importance lies in reducing the likelihood of work-related injuries and improving overall workplace safety. By prioritizing higher-level controls like elimination and substitution, the hierarchy helps employers address hazards at their source, minimizing reliance on less effective measures. This framework not only protects employees but also ensures compliance with legal and regulatory requirements. Additionally, it fosters a culture of safety and proactive risk management within organizations. Implementing this hierarchy is essential for creating a sustainable and injury-free work environment, ultimately benefiting both employees and employers by reducing costs and enhancing productivity.
The Levels of the Hierarchy
The Manual Handling Hierarchy of Control outlines a systematic approach to managing risks, emphasizing elimination, substitution, engineering controls, administrative controls, and PPE to ensure a safer work environment.
2.1 Elimination
Elimination is the highest level of the Manual Handling Hierarchy of Control, focusing on removing the hazard entirely to prevent injury risks. This involves identifying tasks that require manual handling and redesigning processes to eliminate the need for such actions. For example, replacing heavy objects with lighter alternatives or automating tasks can significantly reduce manual handling hazards. Elimination is the most effective control measure as it removes the risk at its source, ensuring a safer work environment. While not always feasible, prioritizing elimination minimizes reliance on lower-level controls like PPE. It encourages proactive problem-solving and is often the first step in implementing a comprehensive risk management strategy.
2.2 Substitution
Substitution is the second level in the Manual Handling Hierarchy of Control, focusing on replacing hazardous manual handling tasks with safer alternatives. This involves identifying tasks that cannot be eliminated and substituting them with equipment or methods that reduce the risk of injury. For example, using mechanical aids like hoists or trolleys to handle heavy loads instead of manual lifting. Substitution aims to minimize physical strain and reduce the likelihood of musculoskeletal disorders. It is a cost-effective and practical solution when elimination is not feasible. By substituting high-risk tasks, employers can create a safer working environment while maintaining productivity. This approach aligns with the hierarchy’s goal of prioritizing higher-level controls to achieve optimal risk reduction.
2.3 Engineering Controls
Engineering controls are physical solutions designed to minimize manual handling risks by modifying the work environment or equipment. These controls are implemented after elimination and substitution, targeting tasks that cannot be fully removed or replaced. Examples include ergonomic workstations, mechanical lifting aids, and automated systems that reduce the need for manual effort. Engineering controls aim to reduce physical strain and prevent injuries by creating a safer workspace. They often involve redesigning tools, equipment, or processes to suit the worker’s capabilities. This level is particularly effective in reducing repetitive or high-force tasks, ensuring a more sustainable and injury-free work environment. Proper implementation requires a thorough understanding of workplace dynamics and employee needs.
2.4 Administrative Controls
Administrative controls are policies and procedures designed to reduce manual handling risks when elimination, substitution, or engineering controls are not feasible. These measures focus on managing work practices, scheduling, and training to minimize exposure to hazardous tasks. Examples include implementing safe work procedures, task rotation, and employee training programs. Administrative controls also involve monitoring workload and ensuring adherence to safety guidelines. While they are less effective than physical controls, they play a crucial role in managing residual risks. Proper implementation requires clear communication, consistent enforcement, and regular updates to reflect workplace changes. These controls are essential for creating a safety-first culture and ensuring employee compliance with manual handling best practices.
2.5 Personal Protective Equipment (PPE)
Personal Protective Equipment (PPE) is the final level in the manual handling hierarchy of control, used when other measures are insufficient to mitigate risks. Common examples include gloves, back supports, and steel-capped boots. PPE is designed to protect workers from injury when direct handling of objects is unavoidable. However, it is considered the least effective control method, as it does not eliminate the hazard but merely reduces the risk of harm. Employers must ensure PPE is properly fitted, maintained, and used in accordance with safety guidelines. Training employees on the correct use of PPE is essential for its effectiveness. While PPE is a critical component of workplace safety, it should always be the last resort after exploring higher levels of control in the hierarchy.
Implementation Strategies
Effective implementation of the manual handling hierarchy of control requires a systematic approach, involving risk assessments, control measure selection, and employee training to ensure workplace safety and compliance.
3.1 Risk Assessment and Identification
Risk assessment and identification are critical steps in implementing the manual handling hierarchy of control. They involve systematically identifying tasks that pose a risk of injury and evaluating factors such as task demands, workload, and individual capabilities. This process ensures that potential hazards are recognized early, allowing for proactive measures to mitigate risks. By conducting thorough assessments, organizations can prioritize interventions and allocate resources effectively. Accurate identification of risks also informs the selection of appropriate control measures, ensuring a targeted approach to workplace safety. Regular reviews and updates to risk assessments are essential to adapt to changing work environments and maintain compliance with safety standards.
3.2 Control Measure Selection
Control measure selection is a critical step following risk assessment, focusing on choosing the most effective interventions to minimize manual handling risks. The hierarchy of control guides this process, prioritizing elimination and substitution as the most effective measures. Engineering controls, such as mechanical aids, are next, followed by administrative controls like task redesign or workload management. Personal Protective Equipment (PPE) is considered a last resort. The selection process must consider feasibility, cost, and worker input to ensure practical and sustainable solutions. Regular monitoring and evaluation of these measures are essential to ensure their effectiveness and adaptability to changing work conditions. Proper documentation and communication of selected controls are also vital for compliance and accountability.
3.3 Employee Training and Awareness
Employee training and awareness are essential for effectively implementing the manual handling hierarchy of control. Workers must be educated on the risks associated with manual handling tasks and trained in safe practices. This includes understanding proper lifting techniques, load assessment, and the use of control measures. Training programs should also emphasize the importance of reporting hazards and near-misses. Employers must ensure that employees are aware of their roles in maintaining a safe work environment and are competent in using equipment and tools provided. Regular refresher training and updates on new procedures or equipment are crucial to sustain a culture of safety. Supervisors should lead by example, reinforcing training principles and encouraging open communication about safety concerns.
Monitoring and Maintenance
Monitoring and maintenance ensure controls remain effective over time. Regular reviews, inspections, and feedback mechanisms help identify gaps and adapt to changing conditions, maintaining workplace safety standards.
4.1 Regular Reviews and Updates
Regular reviews and updates are crucial to ensuring the long-term effectiveness of manual handling controls. Organizations should conduct periodic assessments, ideally annually, to evaluate the continued relevance and efficacy of implemented measures. These reviews involve monitoring incident rates, reassessing risks, and updating control strategies as needed. Feedback from employees and observations of work practices provide valuable insights, helping to identify gaps or areas for improvement. Updates may involve adopting new technologies, revising procedures, or enhancing training programs. Documentation of these reviews ensures accountability and traceability, while also demonstrating compliance with legal standards. Regular reviews foster a proactive approach to workplace safety, ensuring controls remain aligned with evolving operational demands and risks. This iterative process is essential for sustaining a safe and efficient work environment.
4.2 Feedback Mechanisms
Feedback mechanisms are essential for identifying strengths and weaknesses in manual handling controls. They provide a channel for employees to share observations, concerns, and suggestions, fostering continuous improvement. Regular surveys, suggestion boxes, and safety meetings are common methods to gather feedback. Supervisors and safety officers should actively engage with employees to understand their experiences and challenges. This feedback is then analyzed to identify trends or recurring issues, enabling targeted adjustments to control measures. Encouraging open communication helps build trust and ownership among employees, making them more likely to adhere to safety protocols. Feedback mechanisms also highlight the effectiveness of existing controls and guide future enhancements, ensuring the hierarchy of control remains relevant and impactful in reducing manual handling risks. Regular feedback loops ensure proactive problem-solving and adaptive safety practices.
4.3 Continuous Improvement Practices
Continuous improvement practices are vital for sustaining and enhancing manual handling safety. Regular audits and assessments ensure controls remain effective, while benchmarking against industry standards identifies opportunities for advancement. Organizations should encourage a culture of proactive problem-solving, where employees are empowered to identify inefficiencies and propose solutions. Leveraging emerging technologies, such as ergonomic tools and data analytics, can further refine control measures. Training programs should be updated to reflect best practices and new regulations. By fostering collaboration between departments and stakeholders, organizations can share knowledge and implement innovative strategies. Continuous improvement ensures that the hierarchy of control evolves alongside workplace demands, ultimately reducing manual handling risks and promoting a safer work environment.
Legal and Regulatory Standards
The 1992 Manual Handling Operations Regulations require employers to assess and reduce risks, providing a legal framework for safe manual handling practices in the workplace.
5.1 Relevant Legislation and Guidelines
The Manual Handling Hierarchy of Control is supported by various legal frameworks, such as the 1992 Manual Handling Operations Regulations, which mandate employers to assess and mitigate risks. International standards, including EU directives, also provide guidelines to ensure safe practices. Regulatory bodies like the Health and Safety Executive (HSE) issue detailed guidance, outlining steps employers must take to comply. These laws and guidelines emphasize the importance of prioritizing control measures, starting with elimination and substitution, followed by engineering and administrative controls, and finally PPE. Employers are legally required to conduct thorough risk assessments and implement appropriate controls to protect workers from manual handling injuries, ensuring adherence to both national and international safety standards.
5.2 Compliance Requirements
Compliance with manual handling regulations requires employers to implement the hierarchy of control measures effectively. This includes conducting thorough risk assessments to identify manual handling hazards and taking proactive steps to eliminate or reduce risks. Employers must ensure that all control measures, such as engineering solutions or administrative adjustments, are properly implemented and maintained. Training employees on manual handling safety and ensuring their participation in risk management processes is also a critical compliance requirement. Regular audits and reviews of control measures are necessary to maintain compliance and adapt to changing workplace conditions. Failure to meet these requirements can result in legal penalties and increased workplace injury risks, making compliance essential for both legal and ethical reasons.
5.3 Enforcement and Penalties
Enforcement of manual handling regulations is carried out by health and safety authorities, who conduct inspections to ensure compliance with legal standards. Employers who fail to implement the hierarchy of control measures may face penalties, including fines and legal action. The severity of penalties depends on the level of non-compliance and the associated risks. In addition to financial penalties, organizations may face reputational damage and increased insurance costs. Enforcement agencies also provide guidance to help employers understand and meet their obligations. Compliance is not just about avoiding penalties; it is about creating a safer workplace and reducing the likelihood of injuries. Penalties serve as a deterrent to encourage proactive risk management and adherence to legal requirements.
Case Studies and Examples
Real-world examples demonstrate the hierarchy’s effectiveness, such as a hospital reducing injuries by 40% through ergonomic equipment and staff training, showcasing practical applications of control measures.
6.1 Successful Implementation Examples
A manufacturing company significantly reduced manual handling injuries by implementing the hierarchy of control. They started with elimination, removing heavy loads where possible. Substitution followed, replacing manual tasks with automated systems. Engineering controls, such as mechanical aids, were introduced to reduce strain. Administrative controls, like training programs, were enforced to educate employees on safe practices. Finally, PPE was provided as a last resort. This multi-faceted approach led to a 40% reduction in injuries within a year. Regular reviews and feedback mechanisms ensured sustained success. Another example is a healthcare facility that redesigned patient handling procedures, incorporating ergonomic equipment and staff training, resulting in improved safety and productivity.
6.2 Lessons Learned from Failures
Failures in implementing the manual handling hierarchy of control often stem from inadequate risk assessments or neglecting to prioritize higher-level controls. For instance, a warehouse failed to eliminate repetitive lifting tasks, relying solely on PPE, which proved insufficient. This oversight led to increased injuries and compliance issues. Another example is a healthcare facility that skipped substitution and engineering controls, resulting in staff injuries despite extensive training. These cases highlight the importance of systematically applying the hierarchy and not overlooking earlier steps. Organizations must also ensure continuous monitoring and adapt controls as needed. Ignoring employee feedback and failing to update practices regularly exacerbate risks, underscoring the need for a proactive and comprehensive approach to manual handling safety.
6.3 Industry-Specific Applications
The manual handling hierarchy of control is applied across various industries, with tailored approaches to suit specific needs. In healthcare, for example, mechanical aids and ergonomic equipment are prioritized to reduce patient lifting. Manufacturing sectors focus on engineering controls like automated systems to minimize manual tasks. Logistics and retail industries often implement administrative controls, such as job rotation and task redesign, to manage repetitive handling. Construction sites emphasize PPE and training due to dynamic work environments. Each industry adapts the hierarchy to address unique risks, ensuring a balanced approach between elimination, substitution, and engineering solutions. This flexibility highlights the framework’s universal relevance and effectiveness in diverse operational settings, ultimately reducing injuries and enhancing productivity across sectors.
Best Practices and Future Trends
Best practices emphasize ergonomic design and employee training, while future trends focus on emerging technologies like AI and wearable devices to enhance manual handling safety and efficiency.
7.1 Current Best Practices
Current best practices in manual handling emphasize a proactive approach to risk management. Employers should prioritize ergonomic design and task analysis to minimize physical strain. Regular employee training is essential, ensuring workers understand proper techniques and control measures. Continuous improvement practices, such as reviewing incident reports and updating procedures, are also critical. Implementing a combination of engineering and administrative controls is recommended to maximize effectiveness. Encouraging employee feedback and fostering a safety-first culture further enhances compliance and reduces injury risks. These practices align with legal standards and industry guidelines, ensuring a comprehensive approach to manual handling safety.
7.2 Emerging Technologies and Innovations
Emerging technologies are transforming manual handling safety by introducing innovative solutions. Wearable devices, such as sensors and exoskeletons, are being integrated to monitor and reduce physical strain. AI-driven systems can analyze tasks in real-time, providing feedback to prevent unsafe practices. Robotics and automation are increasingly used to eliminate manual lifting in high-risk environments. These technologies not only enhance safety but also improve efficiency and productivity. Additionally, advancements in materials science are leading to lighter and stronger equipment, reducing the physical demands of manual tasks. These innovations are reshaping the manual handling hierarchy, offering new ways to mitigate risks and create safer workplaces. They complement traditional controls while paving the way for a future-focused approach to injury prevention.
7.3 The Role of Technology in Enhancing Controls
Technology plays a pivotal role in enhancing manual handling controls by providing innovative tools to mitigate risks. IoT sensors and real-time monitoring systems enable employers to track workplace conditions and identify potential hazards; AI-powered algorithms analyze data to predict unsafe practices, allowing proactive interventions. Wearable devices, such as smart gloves and sensors, provide immediate feedback to workers about improper lifting techniques. Automation and robotics further reduce manual handling by taking over tasks that involve heavy lifting or repetitive motions. Additionally, digital training platforms ensure employees are well-informed about best practices. These technological advancements not only strengthen the hierarchy of control but also foster a culture of safety and continuous improvement in the workplace.
The Manual Handling Hierarchy of Control effectively reduces workplace injuries by prioritizing elimination, substitution, and engineering controls. Continuous improvement and adherence to legal standards are essential for long-term safety.
8.1 Summary of Key Points
The Manual Handling Hierarchy of Control provides a structured approach to minimizing workplace injuries. It prioritizes eliminating hazards, substituting tasks, and applying engineering controls. Administrative measures and PPE are secondary but crucial. Effective implementation requires risk assessments, employee training, and continuous monitoring. Legal compliance and industry-specific adaptations ensure robust safety frameworks. Case studies highlight successful strategies and lessons learned. Best practices emphasize proactive management and leveraging technology. Ultimately, this hierarchy is essential for creating safer work environments and reducing manual handling risks effectively.